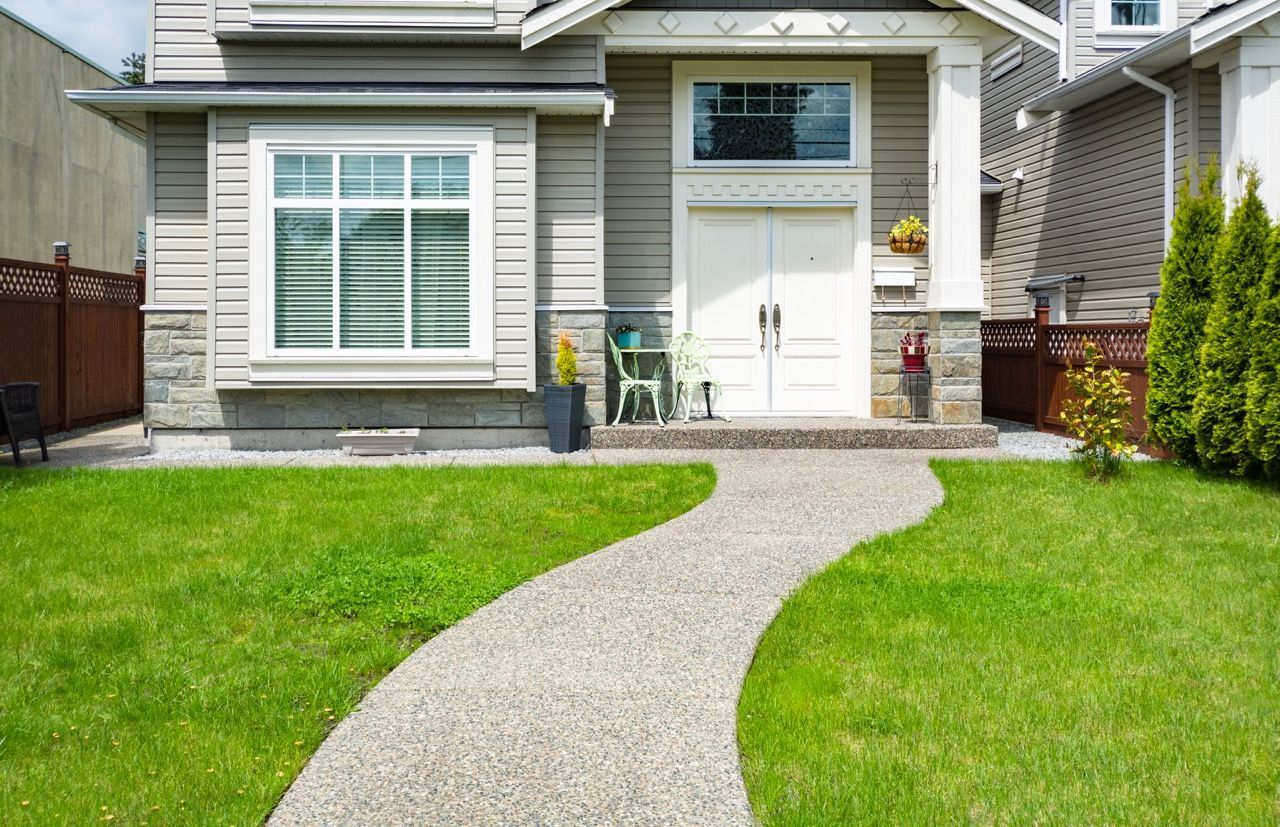
Find out why these common claims about mudjacking are just plain false.
iPhone and Android. Coke and Pepsi. Nike and Adidas.
Some things in life achieve the same goal but are just different. And these differences can be pretty polarizing.
This is even true for concrete leveling. The different concrete leveling methods – stone slurry grout leveling, polyjacking, and mudjacking – all lift concrete back up to a level position for a fraction of the cost of concrete replacement.
But companies often pit these concrete leveling methods against each other by claiming that only one is the real winner – the same way we all know Coke is better than Pepsi, right?
While we here at A-1 Concrete Leveling almost always suggest stone slurry grout leveling for most repairs, our completely unbiased opinion is that mudjacking and polyjacking are also good options for lifting settled concrete back up to a level, even position.
In order to give you a clearer picture of what concrete leveling can really do, we’re borrowing Mythbuster Jamie’s beret and getting to the bottom of the misinformation associated with each method, starting with five mudjacking myths we hear way too often.
Myth #1: Mudjacking Material Weighs Down the Soil
Claim:
The mudjacking material is heavy and weighs down the soil underneath the lifted concrete, causing it to resettle.
This myth is often used to sell polyjacking services, which use a much lighter foam to lift the concrete.
Busted:
In short, soil erosion, natural compaction under newer concrete slabs, and underground pests are what will cause any and most concrete to resettle. Not the weight of the leveling material added during the repair.
Mudjacking materials do weigh more than polyurethane foams, but it’s usually insignificant when considering how heavy the concrete is itself.
The average non-reinforced 4x4-foot sidewalk slab weighs at least 700 pounds, while the average 10x10-foot driveway slab weighs at least 4,375 pounds.
The concrete itself weighs far more than whatever material is placed beneath the slab. If something that heavy is already on top of the soil, the leveling material is not going to weigh it down more in a meaningful way.
It’s also important to point out that even lighter material, like polyurethane foam used for foam concrete leveling, will still distribute the heavy load of the 700+ pound concrete slab down to the soil, even if the lifting material itself weighs less.
If the underlying soils have compacted fully and you’ve dealt with any erosion problems, regardless of which concrete leveling method is used to lift the concrete, the concrete could stay in place for the life of the slab itself without resettling. And that’s cause for celebrating with a Coke (or a Pepsi, if that’s your thing).
Myth #2: Mudjacking Doesn’t Come With a Warranty
Claim:
Because mudjacking repairs are not “built to last,” no contractor will warranty the work.
Busted:
Mudjacking can last for the life of the concrete itself with proper maintenance, and many mudjacking contractors provide multi-year warranties.
The unspoken reality of warranties is that they are more about managing cost vs. risk and are often influenced by market competition. Warranties given for longer amounts of time may inflate repair prices to offset potential claims over time. Knowing a company’s reputation for taking care of its customers and whether it will stand behind its work matters far more than any warranty it may offer.
Also, once injected under the concrete, every leveling method will be exposed to the same factors that can cause all concrete leveling to fail (natural soil compaction, water erosion, pests, etc.) no matter the warranty.
Myth #3: Mudjacking Repairs Have to Be Redone
Claim:
The mudjacking material isn’t hydrophobic, or water-resistant, so exposure to water and erosion means that mudjacking is destined to fail. You may have to get mudjacking repairs redone within 2-5 years.
Busted:
You may be noticing a theme here… specifically with soil and water. Now you’re wearing the beret.
All concrete leveling methods are at risk for erosion due to exposure to water because what really gets eroded away is the soil underneath, not the lifting material itself.
As long as you maintain the mudjacking repair by preventing soil erosion, it could last the life of the concrete itself.
Some ways to combat soil erosion are:
- Caulking concrete joints and cracks
- Keeping soil levels up around the slab
- Preventing excess runoff and drainage around the slab
This is the same for stone slurry grout leveling, polyjacking, and mudjacking – concrete leveling repairs are only as good as the soil they’re sitting on.
Myth #4: Mudjacking Drill Holes Can Cause Concrete to Crack
Claim:
The larger drill hole size used for mudjacking can compromise the structural integrity of the concrete slab, causing it to crack.
Busted:
For quick reference, the average drill hole diameters for concrete leveling repairs are:
- Mudjacking: 2 inches (soda can)
- Stone Slurry Grout Leveling: 1 inch (quarter)
- Polyjacking: ⅝ inch
Drilling Holes Usually Doesn't Cause Cracking
In short, the risk of cracking due to drilling holes (of any size) during the concrete leveling process is very small. If it does happen, it’s likely only going to be in extremely small pieces of concrete, which is typically discussed during the estimation process.
The big drill holes vs. little drill holes used in concrete leveling are more of an aesthetic thing rather than a structural or cracking risk.
The real risks for cracking during the concrete leveling process relate to the quality of the concrete itself and whether or not it’s reinforced. Higher-quality original concrete with reinforcement (wire mesh, rebar) is less likely to experience cracking during the concrete leveling process.
What Can Cause Cracking While Mudjacking
Cracking can occur during a mudjacking repair due to the pressure and volume at which the materials are injected under the slab. In some cases, the materials cannot spread quickly enough so they stress the concrete to the point of cracking.
Additionally, both mudjacking and polyjacking are prone to a pyramiding effect of the materials when they are pumped under the concrete, meaning there are places where the slab is unsupported. As a result, the stress on the concrete between those supported places can lead to cracking.
The stone slurry grout leveling process, on the other hand, is intended to combat material pyramids and other issues caused by the higher pressures used in the mudjacking process. The void beneath the concrete slab is strategically filled while lifting to minimize the chances of future cracking.
“Hey! This article is about mudjacking, not your stone slurry grout leveling process!”
You’re right. Hold onto your *beverage of choice* because things are about to get… messy.
Myth #5: Mudjacking Leaves Behind a Mess
Claim:
The mudjacking compound can get everywhere, spill, and cause a big mess.
Busted:
During the mudjacking process, it may look messy but because the materials are all-natural they can simply be washed off of the concrete.
Experienced mudjacking technicians can keep the mess down the majority of the time unless something unexpected occurs, like hose failure, spilling, or the need for technicians to move around the property more. But even then, the mess due to these unexpected hiccups can be easily washed away with water.
Chemical foams, on the other hand, are much more difficult to clean up. Foam that comes up through cracks or joints and is exposed to the UV rays of the sun will turn yellow. The only way to remove this yellow staining from foam is to either grind or sandblast it away.
Next Steps
While mudjacking vs. polyjacking likely won’t be the new iPhone vs. Android any time soon, these concrete leveling methods, alongside stone slurry grout leveling, can help transform your concrete for a fraction of the cost of replacement.
Now that we can set the beret down and enjoy our Coke, Pepsi, or whatever – we still recommend you continue researching mudjacking and all of the other concrete leveling options. Below we’ve provided some great articles to explore from our online resource library, Concrete Academy:
- What Is Mudjacking?
- Mudjacking: The Pros and Cons
- All About Stone Slurry Grout Leveling
- Stone Slurry Grout Leveling: The Pros and Cons
- All About Foam Concrete Leveling (Polyjacking)
- Foam Concrete Leveling: The Pros and Cons
If you’re ready to see what concrete leveling can do for your settling concrete, click the link below to request an onsite estimate with a member of the A-1 team!
Click Here to Find Your Nearest Location and Receive a FREE Estimate
Sarah Etler joined A-1 Concrete Leveling after receiving her Bachelor of Arts degree in English from Northern Kentucky University. As A-1's Content Marketing Manager, she works closely with industry experts to produce content that will best answer questions related to concrete repair and maintenance practices. Sarah loves living a life full of discovery and is excited every day to see what new things she can learn and share with those around her.
Topics: